The logistics sector is under severe strain! For the past years, one crisis has followed another, leaving operators and warehouse managers with scarcely any room to breathe. The pandemic, lockdown and the blockade of the Suez Canal have all highlighted the fragility of the supply chain. And now the fallout from the war in Ukraine is further complicated by the impact of China’s zero-tolerance Covid containment strategy.
The consequences are many and various : shortages of products such as sunflower oil, knock-on effects on other products, panic buying amplified by social media, cascade effects as seen with e.g. electronic components... and then of course we have the absenteeism problem in distribution centres and higher energy prices.
The fact is, we live in a world of extreme volatility where even the near future is almost impossible to predict - a world where supply chain are increasingly complex. The term we use to describe such a world is VUCA (for Volatility, Uncertainty, Complexity, and Ambiguity).
So what are the implications for warehouse management and how do we deal with them? What avenues should we explore if we are to be ready for all possible risks and disruptions while continuing to better meet the requirements of our customers?
Distribution centres under strain
The purpose of a distribution centre is to receive and store products and deliver them to customers. Depending on the industry sector, it may work with varying delivery schedules, but these tend to be tighter all the time.
The distribution centre is part of a global, multi-level supply chain, and obviously one its primary tasks is to deliver the product to the end customer or local store.
Logistics in VUCA conditions means dealing with spikes in demand over very short periods of time, sometimes followed by equally abrupt slumps. The lean supply chain model has been severely challenged, but it remains very difficult to properly estimate stock volumes. These rapid fluctuations are not only due to shortages. Consumers are now accustomed to a wide variety of products and micro-collections, especially for environmental reasons.
We have to be able to switch to other logistics channel (e-commerce in the case of store closures) at very short notice. Long-term planning is becoming a perilous, and sometimes even useless, exercise. Various constraints, including those of an environmental nature, force the sector to review its distribution models and therefore the location and size of warehouses. This is a particularly delicate exercise for logistics professionals.
Agility, resilience, tolerance to breakdowns: all of these terms take on a very concrete meaning. There are no quick fixes, of course, but in this article we offer some interesting threads for reflection.
Placing our faith in track and trace
We live in an increasingly health-conscious world. Manufacturing processes are more and more stringently controlled, and if a problem arises a product may need to be withdrawn from sale as quickly as possible.
Track and trace also allows us to better inform our customers, ensure regulatory compliance, and minimize errors.
All processes must be analysed: not just picking, but also restocking and inventory. At Scallog, we routinely organize workshops to analyse your processes.
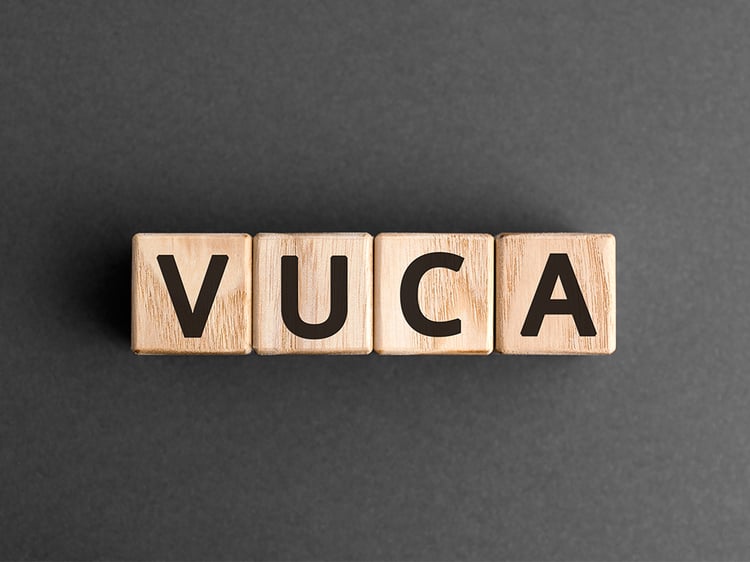
Improving reverse logistics
Managing returns (or reverse logistics) can often be a massive headache. Yet more and more customers are returning products, especially in the clothing sector.
Combined with track and trace, good reverse logistics management allows you to store small quantities without mixing batches, and to optimize use of space and time. If no suitable process is in place, returns too often end up in the dustbin.
Grouped workstations
Faced with absenteeism and load spikes, distribution centre managers regularly recruit temporary staff. In some regions, it's difficult to find competent staff and turnover can be high.
Improving the ergonomics of the workstations therefore has to be a priority. A goods-to-man system has the added advantage of allowing workstations to be grouped in a relatively small space. This configuration simplifies the work of the team leader, who can more easily train and monitor new recruits. No need to tail them around the whole warehouse to make sure the work is done right.
Adapting storage space to requirements
Demand fluctuation, knock-on effects on other products, reverse logistics: all these requirements of VUCA logistics require us to adapt storage space according to our needs. Scallog’s mobile shelf units offer unrivalled flexibility:
- Storage compartments can be different sizes,
- All track and trace operations are handled by special software, which also prevents batches from getting mixing up in the case of returns,
- New shelf units can easily be added and spatial arrangements reconfigured,
- To increase picking capacity, just add robots. Extra robots can even be rented to cover spot requirements,
- Workstations can be used for order picking and management of returns
Time to totally overhaul your distribution centre? Do what Decathlon did, and relocate an entire zone in a matter of hours. And if you’re building a new warehouse, you can even relocate the entire facility.
Order picking in Decathlon fulfilment centre - © Scallog /Decathlon
Using technology as a lever
Our solution is so flexible that some logistics professionals choose the Scallog before even knowing which products it will manage. A facility modernized with Scallog technology will serve to convince their customers of their ability to meet the expectations of end consumers.
Automated order picking is often associated with large investments that take a long time to pay off. In a VUCA context, however, logistics professionals have to aim for very rapid ROI: therefore they have to be able to get an installation up and running very quickly (in a few months) and, if necessary, validate the benefits before proceeding to general rollout. This is exactly what our "Starter Kit" solution enables, making automation accessible even to SMEs.
Automation improves quality of service and the efficiency of order picking: but technology cannot be the weak point of the installation. At Scallog, we‘ve developed a simple and robust robot based on standard or near-standard components, which makes it easier to maintain. Each robot operates independently, which enhances the overall robustness of the installation.
In a VUCA context, the logistics we need is flexible and able to adjust more quickly to the ever-changing needs of clients and consumers.
Laisser nous votre commentaire